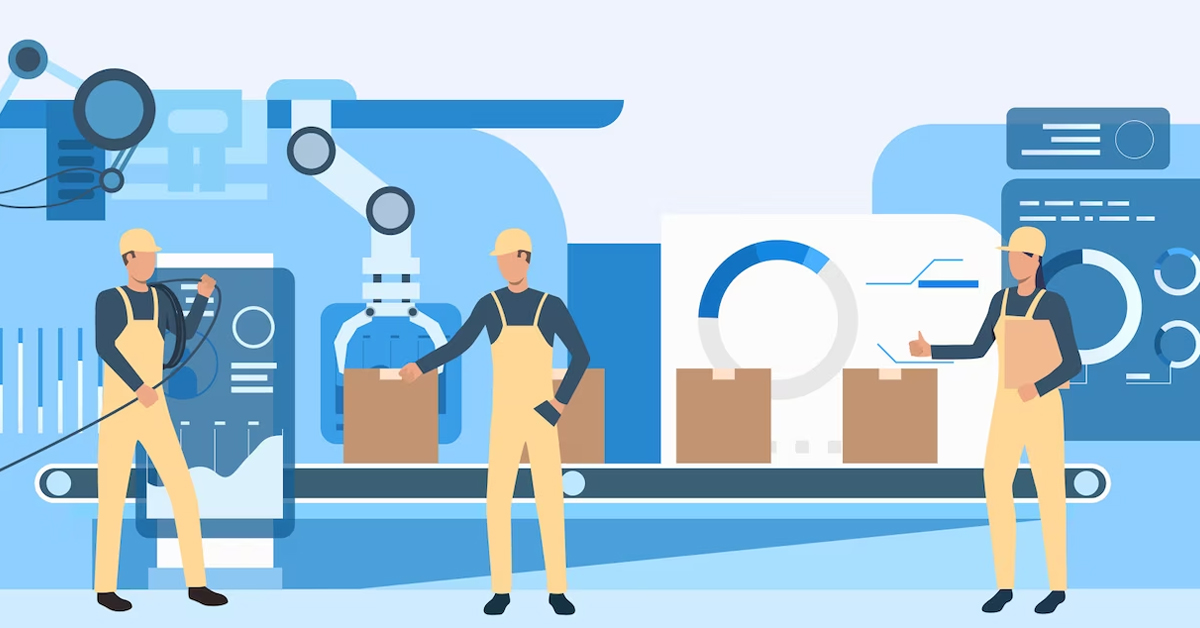
Cắt giảm chi phí là một việc làm nhạy cảm, có thể gây ra nhiều hậu quả nếu cắt giảm sai. Mô hình Lean sẽ giúp doanh nghiệp sản xuất cắt giảm chi phí đúng cách.
Ngành sản xuất những năm gần đây phải đối mặt với nhiều biến động, thúc đẩy các doanh nghiệp coi trọng “cắt giảm chi phí” hơn là “tăng doanh thu”. Một khách hàng của chúng tôi đã từng chia sẻ với Base: “Trong sản xuất, chỉ cần cắt giảm 1% chi phí cũng là điều rất quý”.
Tuy nhiên, cắt giảm chi phí không phải điều dễ dàng. Cắt giảm sai có thể gây ảnh hưởng xấu đến chất lượng sản phẩm, suy giảm doanh thu, kéo tụt hiệu suất người lao động,…
Cắt giảm chi phí đúng cách là việc doanh nghiệp không lãng phí thời gian, nguyên vật liệu, nhân sự vào các hoạt động không cần thiết; hay sản xuất quá mức gây dư thừa và tăng chi phí lưu trữ, kho bãi – đây chính là điều mà mô hình Lean, một mô hình kinh điển trong quản lý vận hành, hướng đến.
Trong bài viết sau đây, Base.vn sẽ đi sâu về ứng dụng mô hình Lean để cắt giảm chi phí trong doanh nghiệp sản xuất, cùng một số case study để doanh nghiệp tham khảo thêm. Hãy cùng theo dõi.
1. Tổng quan về mô hình Lean
1.1 Lean là gì?
Lean là mô hình quản trị theo triết lý tinh gọn, bắt đầu xuất hiện từ lĩnh vực sản xuất và dần được ứng dụng rộng rãi trong nhiều ngành nghề khác nhau. Mô hình này dựa trên ý tưởng tăng năng suất và giảm lãng phí trong sản xuất.
1.2 Nguồn gốc
Trở lại vào những năm 1980, các công ty sản xuất phương Tây nhận ra rằng họ đang nhanh chóng đánh mất thị phần vào tay các công ty sản xuất Nhật Bản. Vì vậy, một cuộc nghiên cứu sự khác biệt giữa Toyota – công ty sản xuất ô tô hàng đầu Nhật Bản, với các nhà sản xuất khác đến từ Mỹ và Châu Âu đã được mở ra. Kết quả cuộc nghiên cứu chỉ ra việc Toyota tập trung vào “loại bỏ tối đa các lãng phí và thời gian trong sản xuất” để tăng lợi nhuận, thay vì sản xuất hàng loạt ồ ạt. Từ đó thuật ngữ Lean Manufacturing (gọi tắt là Lean) hay Toyota Production System – sản xuất tinh gọn đã ra đời.
1.3. Khác biệt giữa mô hình Lean và mô hình sản xuất truyền thống
Khác nhau | Sản xuất truyền thống | Sản xuất Lean |
Triết lý | Tập trung vào sản xuất hàng loạt và tối đa hóa sự sẵn có của tài nguyên. | Tập trung vào tạo ra giá trị cho khách hàng, loại bỏ lãng phí và tối ưu hóa quy trình sản xuất. |
Chiến lược | Sản xuất được thúc đẩy bởi dự báo doanh số (Chiến lược đẩy). | Sản xuất được thúc đẩy bởi nhu cầu của khách hàng (Chiến lược kéo). |
Tầm nhìn và mục tiêu | Tập trung vào lợi nhuận ngắn hạn và tăng cường năng suất. | Tầm nhìn dài hạn, tạo ra giá trị cho khách hàng, tăng cường chất lượng, giảm thiểu lãng phí và tạo ra một môi trường làm việc tốt hơn. |
Quy trình sản xuất | – Quy trình sản xuất tĩnh, không linh hoạt, với sự tách rời giữa các công đoạn sản xuất. – Các quy trình chuẩn hóa chỉ nằm ở trên giấy, thực tế triển khai thì có không thật sự giống. – Bán thành phẩm (WIP) được coi là bình thường trong quy trình sản xuất. | – Quy trình sản xuất linh hoạt, kết hợp các công đoạn lại với nhau, tạo điều kiện cho dòng chảy liên tục và tránh lãng phí. – Có phương pháp để kiểm soát các quy trình thực tế thực hiện đúng và đồng bộ như mẫu chuẩn trên giấy. – Bán thành phẩm được coi là dấu hiệu của quy trình cần cải thiện, là một loại lãng phí cần loại bỏ. |
Đổi mới và cải tiến | – Các vấn đề xảy ra bị nhìn nhận một cách tiêu cực. – Nếu quy trình hiện tại đang chạy ổn định thì doanh nghiệp sẽ không thay đổi. – Tập trung đào tạo con người để giảm sai lỗi. | – Các vấn đề được coi là cơ hội để cải tiến. – Doanh nghiệp cải tiến các quy trình và con người một cách liên tục. – Tập trung cải tiến quy trình để giảm sai lỗi. |
2. 5 nguyên tắc của Lean giúp cắt giảm chi phí trong doanh nghiệp sản xuất
Lean giải quyết doanh nghiệp cắt giảm chi phí như thế nào? Tại sao giữa vô vàn các phương pháp cắt giảm chi phí, Lean lại quen thuộc với các doanh nghiệp sản xuất hơn cả?
5 nguyên tắc cốt lõi tạo nên Lean sẽ trả lời câu hỏi này:
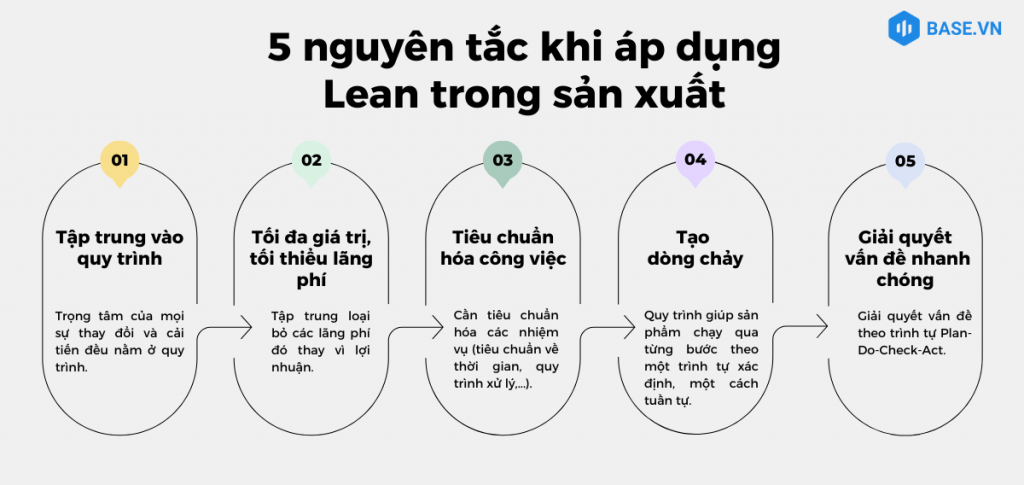
- Nguyên tắc 1 – Tập trung vào quy trình: Trọng tâm của mọi sự thay đổi và cải tiến trong phương pháp Lean đều nằm ở quy trình. Đối với doanh nghiệp sản xuất, các quy trình rất quan trọng bởi nó sẽ quyết định nguồn lực sử dụng, thời gian sử dụng và chất lượng sản phẩm.
- Nguyên tắc 2 – Tối đa giá trị, tối thiểu lãng phí: Trong Lean, các lãng phí được định nghĩa là những hành động không tạo ra giá trị. Phương pháp Lean tập trung loại bỏ các lãng phí đó, đồng thời tăng cường giá trị mang lại cho khách hàng để tạo ra lợi thế cạnh tranh cho doanh nghiệp; thay vì hướng doanh nghiệp tăng lợi nhuận/sức mạnh bằng cách chi nhiều hơn.
- Nguyên tắc 3 – Tiêu chuẩn hóa công việc: Trong Lean, doanh nghiệp sẽ cần tiêu chuẩn các nhiệm vụ (tiêu chuẩn về thời gian, kết quả, quy trình xử lý,…). Khi tiêu chuẩn hóa, doanh nghiệp sẽ đạt được kết quả là chất lượng sản phẩm nhất quán, giảm các chi phí gây ra do sản phẩm lỗi.
- Nguyên tắc 4 – Tạo dòng chảy: “Dòng chảy” có nghĩa là một quy trình mà trong đó sản phẩm chạy qua từng bước theo một trình tự xác định, một cách tuần tự, theo tốc độ yêu cầu của khách hàng. Khi điều này được đạt được, doanh nghiệp giảm thiểu những yếu tố phát sinh có thể gây lãng phí trong quy trình, giảm thiểu thời gian chờ và tăng tính linh hoạt cho quy trình.
- Nguyên tắc 5 – Giải quyết vấn đề nhanh chóng: Trong Lean, chúng ta nhìn nhận vấn đề như cơ hội để cải tiến. Thay vì nhảy vào giải pháp, chúng ta giải quyết các nút thắt theo một trình tự khoa học Plan-Do-Check-Act: Đi từ xác định nguyên nhân gốc rễ của vấn đề, phát triển giải pháp, triển khai giải pháp, kiểm tra kết quả, đến áp dụng phương pháp mới. Nhờ vậy, các nút thắt được tháo nhanh hơn, giúp doanh nghiệp tiết kiệm thời gian và nguồn lực.
Đọc thêm: Kaizen là gì? Hướng dẫn cách triển khai Kaizen trong doanh nghiệp
3. Ứng dụng mô hình Lean nhận diện 8 loại lãng phí trong sản xuất
Ứng dụng mô hình Lean, doanh nghiệp sẽ nhận diện đúng đâu thật sự là những khoản đang gây lãng phí. Khi gọi tên chính xác các lãng phí, doanh nghiệp sẽ có lựa chọn cắt giảm đúng thay vì “cắt nhầm” vào các chi phí thiết yếu, gây ra các thiệt hại không đáng có.
Dựa vào mức độ phổ biến của các lãng phí, Jean Cunningham – đồng sáng lập Lean Enterprise Institute và các cộng sự đã nghiên cứu và đưa ra mô hình tổng hợp 8 loại lãng phí trong sản xuất mang tên D.O.W.N.T.I.M.E:
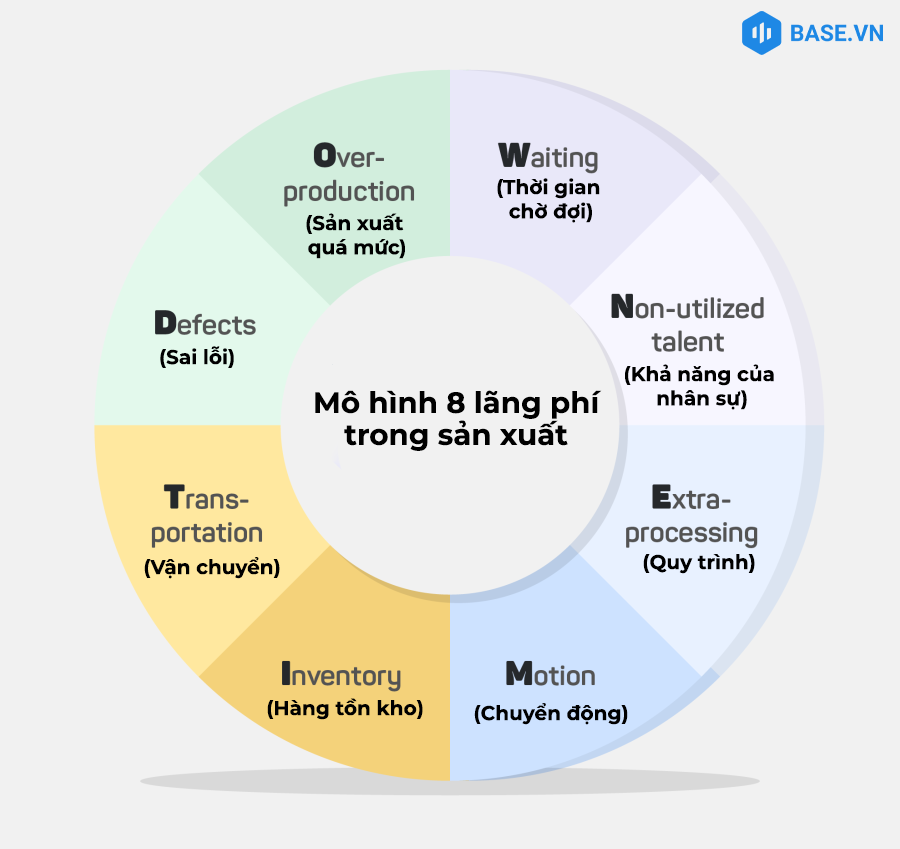
4. Case study ứng dụng mô hình Lean trong sản xuất để cắt giảm chi phí
Nhắc đến doanh nghiệp ứng dụng mô hình Lean thành công thì không thể không kể đến Toyota. Tuy nhiên trừ khi bạn là một nhà sản xuất ô tô toàn cầu và đang tìm cách dẫn đầu thị trường, nếu không việc “copy-paste” những điều Toyota đã làm sẽ không mang lại hiệu quả cho bạn.
Trong phạm vi bài viết, chúng tôi sẽ giới thiệu bạn một doanh nghiệp khác có quy mô vừa và gần gũi với thực tế các doanh nghiệp hơn.
Doanh nghiệp sản xuất sản phẩm kỹ thuật cao theo đơn đặt hàng đã ứng dụng Lean như thế nào để cắt giảm chi phí?
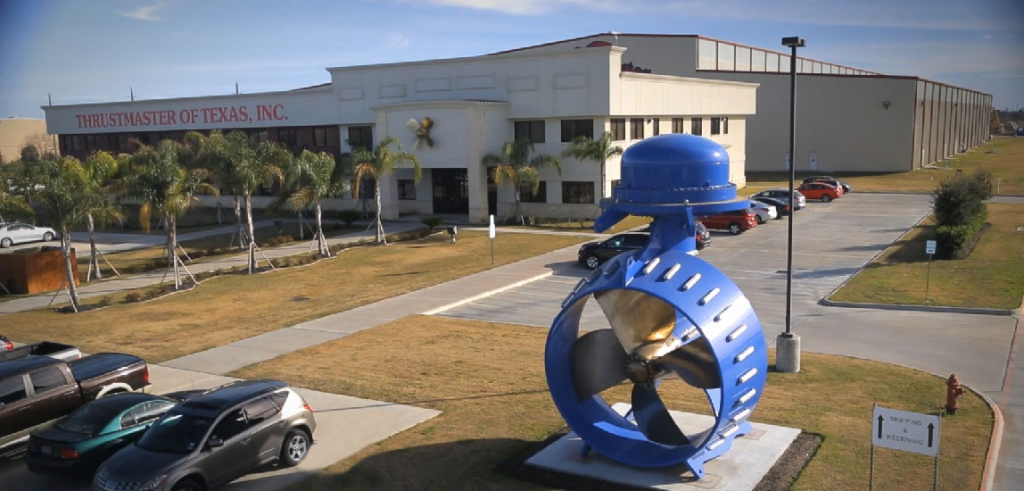
Thrustmaster là một doanh nghiệp sản xuất sản phẩm kỹ thuật cao theo đơn đặt hàng, chuyên sản xuất các loại bánh xe đua phản hồi lực. Trong những năm gần đây khi cảm nhận được sự gia tăng nhanh chóng của nhiều đối thủ cạnh tranh, cùng với đó là sự tăng giá đột ngột của nhiều nguyên vật liệu, Thrustmaster đặt ra các mục tiêu nhằm củng cố lợi thế cạnh tranh, đó là:
- Cải thiện chất lượng sản phẩm.
- Tăng tỷ lệ giao hàng đúng hạn.
- Giữ nguyên giá thành sản phẩm bằng cách cắt giảm hoặc ổn định chi phí luôn nằm trong mức dự trù ban đầu.
Nhờ sự gợi ý của các chuyên gia cải tiến, Thrustmaster đã triển khai ứng dụng mô hình Lean trong 18 tháng để giải quyết các vấn đề này.
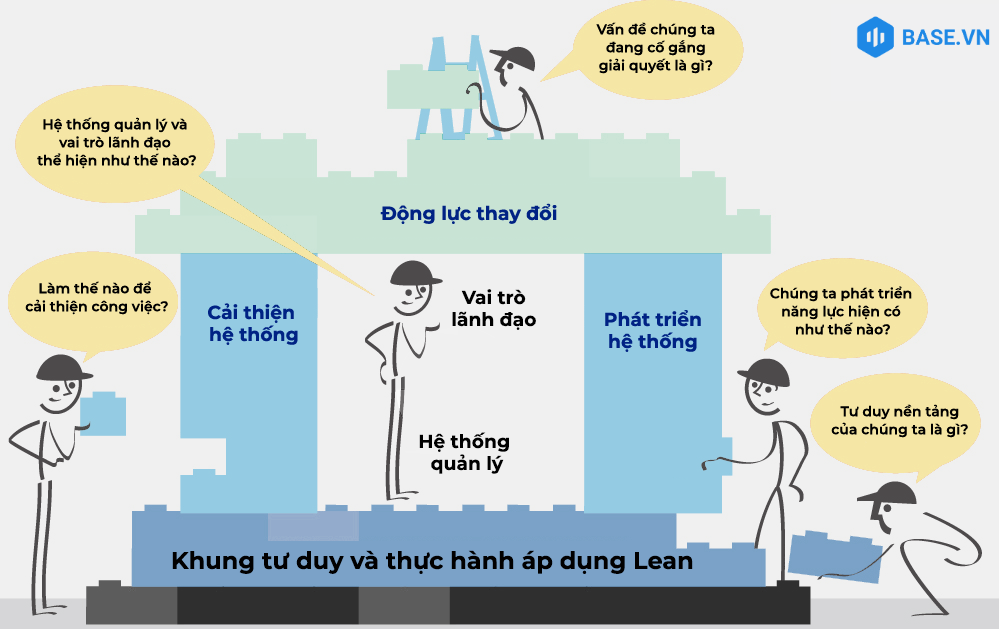
Trước khi bắt tay vào triển khai, doanh nghiệp lập ra một list các câu hỏi cần trả lời:
- Động lực thay đổi:
- Mục tiêu của chúng ta là gì? (Đã trả lời ở trên)
- Vấn đề chúng ta đang cố gắng giải quyết để hiện thực hóa mục tiêu là gì?
- Cải thiện hệ thống:
- Hệ thống quản lý nào phù hợp để giải quyết vấn đề?
- Chúng ta làm thế nào để mang lại những cải thiện?
- Phát triển năng lực:
- Vai trò lãnh đạo
- Chúng ta phát triển năng lực hiện có như thế nào?
– Vấn đề doanh nghiệp gặp phải:
Để tìm ra các vấn đề cần cải thiện, doanh nghiệp đã rà lại tất cả các bước để có một sản phẩm lắp ráp hoàn thiện và thu được một số kết quả:
- Khi theo sát từng quy trình sản xuất, doanh nghiệp nhận ra có rất ít quy trình được thực hiện đúng theo chuẩn, dẫn đến việc cấp quản lý không thể nắm được tình hình sử dụng nguyên vật liệu và tiến độ sản xuất từng mã sản phẩm.
“Chúng tôi không thể phân biệt đâu là sản phẩm dở dang, đâu là hàng tồn kho khi nhìn xung quanh. Cấp quản lý không thể phân biệt được đâu là tình huống bình thường, tình huống bất thường, hay liệu một đội cụ thể đang đúng tiến độ hay chậm tiến độ, một nhân viên có đang làm đúng hay không.” LÃNH ĐẠO THRUSTMASTER CHIA SẺ.
- Tổng thời gian di chuyển các mảnh bộ phận và nguyên vật liệu cần sản xuất mất tới 10 giờ, thời gian này không mang lại giá trị gia tăng cho sản phẩm, tạo ra lãng phí thời gian cho doanh nghiệp.
Đối chiếu với mô hình Lean, ta thấy được có 3 loại lãng phí hiện rõ ở đây đó là:
- Lãng phí từ quy trình: Không thực hiện đúng theo quy trình nên sử dụng nguyên vật liệu không đúng cách, xử lý không đúng cách khiến sản phẩm ra không đảm bảo chất lượng và khiến nhân viên mất nhiều thời gian để xử lý hơn.
- Lãng phí do sai lỗi: Vì doanh nghiệp không kiểm soát được việc xử lý sản phẩm của bên dưới nên rủi ro sản phẩm lỗi hỏng, không đạt yêu cầu cao.
- Lãng phí do vận chuyển: Doanh nghiệp mất quá nhiều thời gian để vận chuyển nguyên vật liệu, bán thành phẩm và đi lại trong nhà máy.
– Hệ thống quản lý phù hợp:
Trước tiên, doanh nghiệp thiết lập lại hệ thống quản lý để quyết định việc cải tiến sẽ bắt đầu theo trình tự nào.
Doanh nghiệp nhận thấy hệ thống quản lý hiện tại đang không phù hợp. Quản lý theo mô hình dây chuyền không phù hợp với đặc thù doanh nghiệp, vì doanh nghiệp sản xuất nhiều mã sản phẩm khác nhau, dù có chung một quy trình xử lý nhưng các bước trong quy trình lại khác nhau.
Thay vào đó, doanh nghiệp thay đổi sang quản lý theo từng mã sản phẩm. Theo đó, doanh nghiệp đã chia nguồn lực/không gian theo các sản phẩm và bố trí không gian/công việc theo quy trình lắp ráp chính, và cải tiến theo từng sản phẩm.
– Những cải thiện của doanh nghiệp:
Sau đó, doanh nghiệp áp dụng những cải thiện mới gồm:
- Chuẩn hóa công việc, quy trình
- Tổ chức lại không gian
- Kiểm soát trực quan
Bước 1: Chuẩn hóa công việc, quy trình
– Vấn đề ở phần này là quy trình lắp ráp luôn phụ thuộc vào kiến thức và kinh nghiệm ngầm của nhân viên. Mặc dù các bước trong quy trình là giống nhau, nhưng các chi tiết ở mỗi bước quy trình sẽ khác nhau tùy vào yêu cầu của khách hàng với mã sản phẩm. Vì không có một quy trình lắp ráp chuẩn và tiêu chuẩn đầu ra nên rất khó để Thrustmaster kiểm soát chất lượng sản phẩm.
– Giải pháp của doanh nghiệp là trước tiên ghi lại chính xác cách nhân viên lắp ráp từng mã sản phẩm. Sau đó doanh nghiệp sắp xếp, phân bổ lại các bước, tiêu chuẩn hóa các bước quy trình lắp ráp theo luồng nguyên liệu, thời hạn hoàn thành.
Bước 2: Tổ chức lại khu vực lắp ráp
Sắp xếp lại không gian lắp ráp
– Trước khi tổ chức lại khu vực lắp ráp, cấp quản lý nhìn vào không theo dõi được tiến độ quy trình ra sao, không thấy được tình trạng xử lý công việc, không phân biệt được bán thành phẩm và thành phẩm.
– Sau khi tổ chức lại khu vực theo trình tự các bước trong quy trình, nhìn vào hình dưới đây ta có thể xác định rõ ràng các khu vực làm việc, tình hình sử dụng xử lý công việc ở từng bước. Vì các thành phẩm sẽ được kéo tiếp sang bước tiếp theo để xử lý nên bán thành phẩm dễ nhìn thấy và đếm được. Đặc biệt, nhờ phân chia các khu vực theo trình tự các bước trong quy trình, doanh nghiệp cắt giảm thời gian di chuyển nguyên vật liệu từ bước này qua bước tiếp.
Sắp xếp lại nguyên vật liệu
– Ngoài ra, doanh nghiệp cũng sắp xếp lại nguyên vật liệu trong xưởng. Trước đây, những nhân viên lắp ráp thường phải tìm kiếm trong mớ hỗn độn các linh kiện được giấu trong hộp carton.
– Ngày nay, các linh kiện cần thiết cho từng bước được chuyển chính xác tới khu vực xử lý bước đó, sau đó được gắn lên trên bảng ghim ngay đó để nhân viên dễ tìm thấy loại linh kiện cần.
– Có thể thấy, việc sắp xếp bố trí lại khu vực làm việc giúp nhân viên tiết kiệm thời gian khi tìm kiếm linh kiện, số lượng linh kiện hiện trên bảng ghim cũng phản ánh được tiến độ lắp ráp của đội.
Lợi ích của việc tổ chức lại khu vực lắp ráp: Các nguyên liệu được sử dụng triệt để, không có sót lại hay bỏ đi. Nhân viên luôn biết được nên làm gì tiếp theo. Nhìn vào không gian làm việc, dù cấp quản lý hay là nhân viên cũng nắm được ngày làm việc năng suất hay kém năng suất.
Bước 3: Quản lý trực quan
Sau khi áp dụng các cải thiện, doanh nghiệp sử dụng hình thức quản lý trực quan bằng bảng biểu, gồm các thông tin: Tình trạng sử dụng máy móc thiết bị, thông số điều chỉnh, các công việc cần làm. Các bảng sẽ được đặt ở mỗi khu vực sản xuất, nhân viên sẽ chủ động cập nhật thông tin lên bảng và cấp quản lý cũng dễ dàng theo dõi được bên dưới xử lý công việc như thế nào.
– Quản lý hoạt động cải tiến:
Doanh nghiệp thành lập ban cải tiến và giao trách nhiệm quản lý thực thi cải tiến bên dưới. Nhiệm vụ của ban cải tiến là đến từng bộ phận để thu thập số liệu từ các bảng biểu, sau đó làm báo cáo đánh giá tình hình thực hiện.
– Phát triển năng lực:
Sau khi thực hiện cải tiến ở quy trình lắp ráp và nhận được hiệu quả, doanh nghiệp đã bắt đầu mở rộng ứng dụng mô hình Lean qua các bộ khác theo trình tự:
- Khảo sát thực tế và đối chiếu với mô hình D.O.W.N.T.I.M.E để tìm ra các lãng phí.
- Xử lý các vấn đề theo vòng lặp Plan Do Check Act: Lên kế hoạch, thực thi, kiểm tra, áp dụng.
- Quản lý việc thực thi chặt chẽ qua các bảng biểu đặt ở các bộ phận; ghi rõ mục tiêu, trách nhiệm từng người, các công việc cần làm.
- Trao quyền cho ban cải tiến quản lý hoạt động cải tiến ở các bộ phận.
– Kết quả:
Sau 18 tháng, Thrustmaster đạt được mục tiêu đã đề ra với các số liệu:
- Tỷ lệ hoàn thành đúng hạn trong lần đầu tiên FPY (First-pass yield) lên 90%.
- Tỷ lệ giao hàng đúng hạn lên 90%.
- Đảm bảo chi phí sản xuất luôn nằm trong mức xác định hoặc ít hơn.
Qua case study này, các doanh nghiệp sản xuất các sản phẩm kỹ thuật cao theo đơn đặt hàng tại Việt Nam có thể biết được một số thông tin hữu ích để ứng dụng Lean hiệu quả trong mô hình của mình.
Đọc thêm: Six Sigma là gì? Cẩm nang 6 sigma dành cho người mới tìm hiểu
5. Làm thế nào để phát huy hiệu quả mô hình Lean trong doanh nghiệp của bạn?
Tùy thuộc vào vấn đề muốn giải quyết mà mỗi doanh nghiệp sẽ có cách thức ứng dụng Lean khác nhau. Tuy nhiên trong những case study ứng dụng Lean thành công nhất – như Thrustmaster, hay Toyota, Nike, Intel,… luôn có mặt 6 yếu tố sau đây:
– Có mục tiêu chiến lược rõ ràng:
Doanh nghiệp cần phải hiểu rõ Lean không phải là một chiến lược, “trở nên tinh gọn” không phải là kết quả. Nói chính xác, Lean là phương pháp để giúp doanh nghiệp đạt được mục tiêu chiến lược.
Để ứng dụng Lean đúng cách, trước hết doanh nghiệp cần có mục tiêu rõ ràng và truyền đạt cho nội bộ thấy tầm quan trọng của các mục tiêu đó. Từ đó, nội bộ cũng sẽ hiểu được vai trò của Lean trong việc giúp doanh nghiệp đạt mục tiêu, vì vậy sẽ chủ động thực hiện Lean.
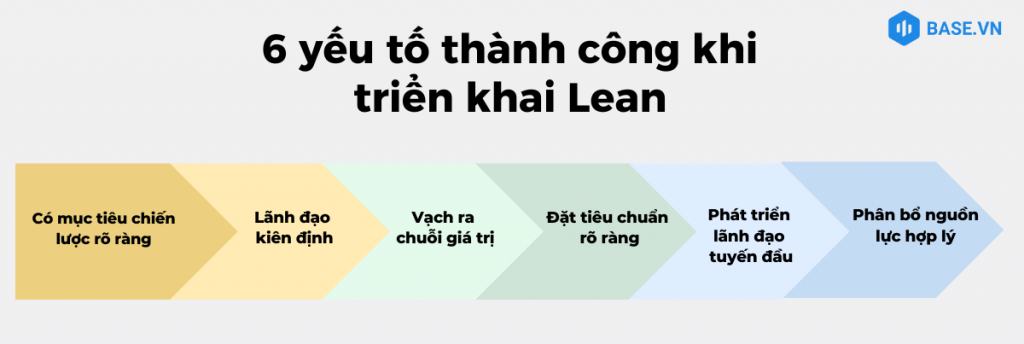
– Lãnh đạo kiên định với Lean:
Có một số lượng lớn các lãnh đạo cho rằng sự tinh gọn Lean không phù hợp với họ. Các nhà lãnh đạo cấp cao cần thể hiện rõ Lean qua các hành vi lãnh đạo, có thể kể đến như: truyền đạt tầm nhìn rõ ràng về ứng dụng Lean; thường xuyên trực tiếp đến các xưởng sản xuất của mình; thể hiện sự tôn trọng của nhân viên tuyến đầu; và khi có vấn đề xảy ra và mọi thứ không như mong đợi, hãy tự hỏi nguyên nhân gốc rễ là gì thay vì ngay lập tức lên án nhân viên.
– Vạch ra chuỗi giá trị:
Chúng ta đã thảo luận về cách Lean tối đa hóa giá trị và loại bỏ lãng phí. Nhưng làm thế nào để bạn nhìn thấy sự lãng phí trong doanh nghiệp của bạn và làm thế nào để bạn quyết định cách tốt nhất để loại bỏ sự lãng phí đó? Câu trả lời đó là vạch ra chuỗi giá trị từ đầu đến cuối, từ khâu nhập nguyên vật liệu thô đến khâu giao thành phẩm. Chuỗi giá trị (nếu sử dụng đúng cách) sẽ hướng bạn đến một lộ trình cải tiến rõ ràng và đơn giản, giúp bạn tránh bị xao nhãng và đi lạc đường.
– Đặt tiêu chuẩn rõ ràng:
Tiêu chuẩn hóa nơi làm việc và bản thân công việc là nền tảng của mô hình Lean. Doanh nghiệp có thể bắt đầu 5S để chuẩn hóa nơi làm việc của bạn, sau đó chuẩn hóa công việc từ những phần việc quan trọng nhất. Đặt tiêu chuẩn rõ ràng ngay từ đầu sẽ ổn định quy trình sản xuất và mang lại chất lượng sản phẩm nhất quán, và đó cũng cung cấp cơ sở để thực hiện các cải tiến khác.
– Phát triển các lãnh đạo tuyến đầu:
Lãnh đạo tuyến đầu được xem như là người có ảnh hưởng lớn nhất về khía cạnh văn hóa trong các quá trình cải tiến như Lean. Họ là quản lý, người giám sát, trưởng nhóm,… là những người mà nhân viên của bạn tin tưởng hơn, lắng nghe hơn và trực tiếp báo cáo công việc hàng ngày. Hãy cung cấp cho họ những công cụ quản lý, đào tạo họ kỹ năng lãnh đạo và những hiểu biết về cải tiến để họ có thể tạo ra nhiều “lực đẩy cải tiến” hơn trong nội bộ.
– Phân bổ nguồn lực hợp lý:
Một vấn đề lớn khiến các doanh nghiệp ứng dụng Lean không thành công là do thiếu nguồn lực, nguồn lực nội bộ không hưởng ứng. Thực tế mọi người trong doanh nghiệp bạn đã rất bận rộn với hàng tá công việc chính được giao hàng ngày và khó có thể hết mình với những hoạt động khác. Dù vậy, doanh nghiệp vẫn cần đảm bảo có đủ nguồn lực để đáp ứng việc này. Doanh nghiệp có thể thuê ngoài các đội tư vấn, chuyên gia, huấn luyện về Lean; đồng thời sử dụng các công cụ phần mềm để giúp việc quản lý thời gian tiện lợi hơn, tốn ít thời gian và sức lực hơn.
6. Tạm kết
Trong ngành sản xuất thì Lean là một trong những giải pháp hàng đầu về cắt giảm chi phí, đã và đang được nhiều doanh nghiệp ứng dụng trong mô hình của mình. Khi tìm đến bài viết này, hẳn doanh nghiệp của bạn đã biết đến Lean, hoặc đã ứng dụng Lean nhưng chưa thật sự thu được hiệu quả mong đợi. Với những kinh nghiệm đúc rút từ những chuyên gia hàng đầu về Lean, cùng case study ứng dụng Lean thành công, hy vọng bài viết đã mang lại những thông tin hữu ích cho quý doanh nghiệp.